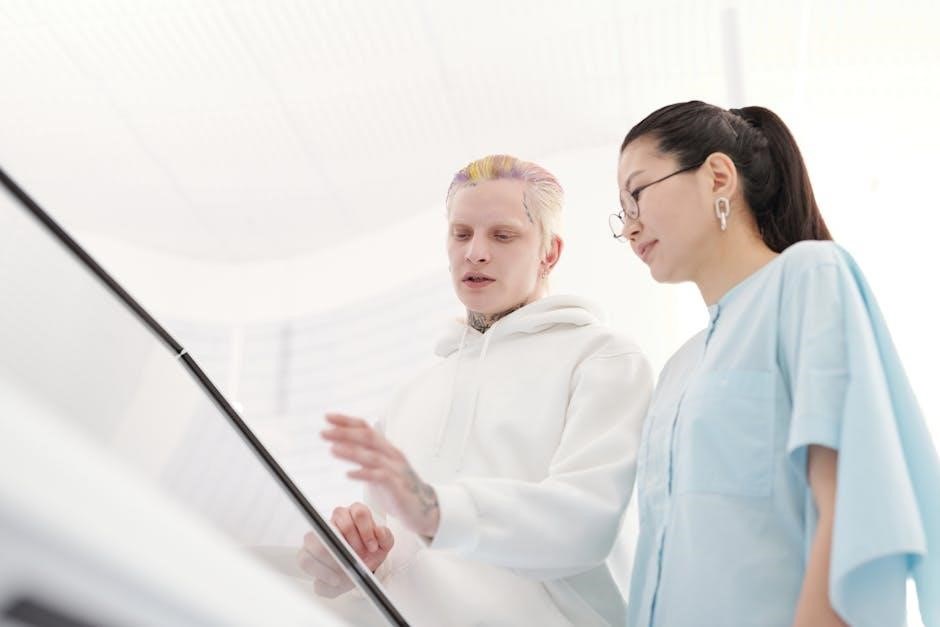
A structured template details step-by-step procedures‚ meeting ISO 9001 requirements and streamlining operations․ Vital in ISO 9001 documentation‚ alongside procedures and process descriptions․ The template includes sections for the company name‚ process number‚ dates‚ version‚ job and project numbers․
In the realm of ISO 9001‚ work instructions serve as detailed guides‚ crucial for consistent execution of tasks․ They bridge the gap between procedures and actual practice‚ providing clarity on how to perform specific activities․ Unlike broader procedures‚ work instructions delve into the operational details‚ offering step-by-step guidance․ This granular approach ensures that employees understand and adhere to standardized methods․
Work instructions are particularly valuable when tasks are complex‚ require specialized skills‚ or have a direct impact on product quality․ By documenting these tasks‚ organizations minimize variability and enhance overall efficiency․ Moreover‚ work instructions facilitate training and knowledge transfer‚ enabling new employees to quickly grasp essential processes․ They also serve as a reference point for experienced staff‚ ensuring adherence to best practices․
The implementation of work instructions demonstrates a commitment to quality management principles; It showcases a proactive approach to process control and continuous improvement․ These instructions are living documents‚ subject to review and revision as processes evolve․ Their accessibility and clarity contribute significantly to a culture of quality consciousness within the organization․
Purpose of Work Instructions
The primary purpose of work instructions is to provide clear and concise guidance on how to perform specific tasks within a process․ They serve as a practical tool for ensuring consistency‚ accuracy‚ and efficiency in daily operations․ By outlining the step-by-step procedures‚ work instructions minimize ambiguity and reduce the risk of errors․ This is particularly important in industries where precision and quality are paramount․
Beyond task execution‚ work instructions play a vital role in training and knowledge transfer․ They provide a standardized resource for new employees‚ enabling them to quickly learn and understand the required processes․ For experienced staff‚ work instructions serve as a reference point‚ ensuring adherence to best practices and promoting continuous improvement․ They also facilitate communication and collaboration among team members‚ fostering a shared understanding of work processes․
Furthermore‚ work instructions contribute to overall quality management by documenting the “how-to” aspects of a quality system․ They provide evidence of controlled processes‚ which is essential for ISO 9001 compliance․ By standardizing work practices‚ organizations can improve efficiency‚ reduce waste‚ and enhance customer satisfaction․ The ultimate goal is to create a culture of excellence‚ where every employee is empowered to perform their tasks effectively and contribute to the success of the organization․
ISO 9001 Requirements for Work Instructions
While ISO 9001 doesn’t explicitly mandate the creation of work instructions for every process‚ it emphasizes the need for documented information to support the operation of processes and ensure consistent product or service conformity․ Clause 7․5․1 b) of ISO 9001 highlights that work instructions may be provided where necessary to ensure the effective planning‚ operation‚ and control of processes․ This implies that if a process requires detailed guidance to achieve desired outcomes‚ work instructions become a crucial element of the quality management system․
The standard requires organizations to maintain documented information to the extent necessary to have confidence that processes are being carried out as planned․ Work instructions fulfill this requirement by providing a clear and detailed description of how a task should be performed․ They serve as evidence of process control and contribute to the overall effectiveness of the quality management system․
Furthermore‚ ISO 9001 requires organizations to control documented information‚ ensuring it is available‚ suitable‚ and protected․ Work instructions‚ as documented information‚ must be properly managed‚ maintained‚ and updated to reflect current practices․ Regular reviews and revisions are necessary to ensure accuracy and relevance․ By adhering to these requirements‚ organizations can leverage work instructions to enhance process performance‚ improve product or service quality‚ and achieve customer satisfaction․
Key Elements of a Work Instruction Template
A well-structured work instruction template is crucial for creating clear‚ concise‚ and effective work instructions that meet ISO 9001 requirements․ The template should incorporate several key elements to ensure consistency and ease of use․ First‚ it should include a title and identification information‚ such as the company name‚ document number‚ revision date‚ and job or project number․ This information helps to track and manage the document effectively․
The core of the template should focus on providing a step-by-step procedure‚ outlining each task in a clear and logical sequence․ Each step should be described with sufficient detail to avoid ambiguity and ensure consistent execution․ The template should also include sections for tools‚ equipment‚ and materials required for the task․ This helps to ensure that all necessary resources are readily available․
Furthermore‚ the template should address competency requirements‚ specifying the skills‚ knowledge‚ and training needed to perform the task effectively․ It is also important to include references to relevant documents and standards‚ such as procedures‚ forms‚ drawings‚ and specifications․ Finally‚ the template should incorporate document control and revision history‚ providing a record of changes and updates made to the work instruction over time․ By including these key elements‚ the template ensures that work instructions are comprehensive‚ accurate‚ and easy to follow‚ contributing to improved process performance and quality outcomes․
Title and Identification Information
The title and identification information section of a work instruction template is paramount for proper document control and traceability within an ISO 9001 quality management system․ This section typically resides at the top of the document and provides essential details for identifying‚ tracking‚ and managing the work instruction effectively․ The title should be clear‚ concise‚ and descriptive‚ accurately reflecting the task or process the instruction covers․
In addition to the title‚ this section should include a unique document number to distinguish it from other work instructions and related documents․ The revision date is crucial for ensuring that the latest version of the instruction is being used․ Including the company name or logo helps to establish ownership and context․ Furthermore‚ fields for the job number and project number can be added to link the work instruction to specific projects or tasks within the organization․
The inclusion of prepared by and reviewed by fields ensures accountability and validation of the work instruction’s content․ All this information collectively provides a comprehensive overview‚ facilitating easy identification‚ retrieval‚ and management of the work instruction‚ which is vital for maintaining quality and consistency in operations․ This foundational information ensures users can quickly understand the document’s purpose‚ scope‚ and validity․
Step-by-Step Procedure
The step-by-step procedure forms the core of any effective work instruction‚ providing a detailed‚ sequential guide on how to perform a specific task․ Each step must be clearly articulated‚ using concise and unambiguous language to minimize any potential for misinterpretation․ Begin with an introductory statement that sets the stage‚ outlining the overall objective of the procedure․ Then‚ break down the process into manageable‚ discrete steps‚ each representing a distinct action․
Number each step sequentially to maintain a logical flow and facilitate easy reference․ Include specific details‚ such as measurements‚ settings‚ or specific actions required at each stage․ Visual aids‚ such as diagrams‚ photographs‚ or flowcharts‚ can significantly enhance clarity‚ particularly for complex or technical tasks․ Use action verbs to clearly convey what needs to be done․ For example‚ “Tighten the bolt” or “Verify the alignment․”
Where applicable‚ include conditional statements to address different scenarios or outcomes․ For example‚ “If the indicator light is green‚ proceed to step 5; otherwise‚ troubleshoot the connection․” Conclude the procedure with a final step that confirms the task’s completion‚ such as “Verify the final product meets the specified criteria․” Ensure that the steps are logical‚ easy to follow‚ and provide sufficient detail to enable a competent operator to perform the task successfully and consistently․
Tools‚ Equipment‚ and Materials
This section meticulously lists all necessary tools‚ equipment‚ and materials required to perform the task outlined in the work instruction․ Clarity and specificity are paramount here to prevent any ambiguity or delays during the execution of the procedure․ For each item‚ provide a detailed description‚ including the name‚ model number‚ size‚ and any other relevant specifications․ This ensures that the correct resources are readily available and minimizes the risk of using incorrect or unsuitable substitutes․
Include information on any required calibration or maintenance for the equipment to guarantee accuracy and reliability․ Specify the quantities of materials needed‚ along with any specific storage or handling instructions․ For tools and equipment‚ indicate any necessary safety precautions or personal protective equipment (PPE) that must be used during operation․ This reinforces a culture of safety and prevents potential accidents or injuries․
Consider including images or diagrams of the tools and equipment for visual clarity‚ especially for less common or specialized items․ Where applicable‚ provide links to suppliers or internal inventory systems to facilitate easy procurement of the required resources․ Regularly review and update this section to reflect any changes in tools‚ equipment‚ materials‚ or suppliers․ This ensures that the work instruction remains accurate and relevant over time․
Competency Requirements
This section clearly defines the necessary skills‚ knowledge‚ and training required for personnel to perform the work instruction effectively and safely․ It outlines the specific competencies individuals must possess before undertaking the task‚ ensuring that they are adequately prepared and capable of achieving the desired outcomes․ These requirements may include formal qualifications‚ certifications‚ specific training courses‚ or demonstrated experience․
Specify any mandatory prerequisites‚ such as area inductions‚ safety training‚ or equipment-specific certifications․ Clearly state the required level of proficiency for each competency‚ whether it’s basic understanding‚ intermediate skill‚ or expert knowledge․ Indicate the methods used to assess competency‚ such as written tests‚ practical demonstrations‚ or performance evaluations․
Identify who is authorized to approve competency achievement‚ such as supervisors‚ trainers‚ or qualified assessors․ Document the process for maintaining competency‚ including refresher training‚ periodic assessments‚ or ongoing professional development․ Regular review and updates to this section are essential to align with evolving job roles‚ technological advancements‚ and regulatory changes․ This ensures that personnel possess the necessary competencies to consistently perform the work instruction to the required standards․
Referenced Documents and Standards
This section meticulously lists all external and internal documents‚ standards‚ and regulations that are directly relevant to the work instruction․ This ensures that users have access to the necessary information for proper execution and compliance․ Accurate and up-to-date references are crucial for maintaining consistency‚ avoiding errors‚ and adhering to industry best practices and legal requirements․
Include the full title‚ document number‚ revision date‚ and source of each referenced item․ This might involve specifications‚ technical manuals‚ safety data sheets (SDS)‚ regulatory guidelines‚ or internal procedures․ Provide hyperlinks or clear instructions on how to access these documents efficiently․
Clearly state the purpose of each reference and how it relates to the specific steps within the work instruction․ For instance‚ a referenced standard might specify the acceptable tolerances for a particular measurement‚ while an SDS provides crucial safety information for handling a specific chemical․ Emphasize the importance of consulting these references before commencing the work and during the process‚ as needed․ Regular review and updates to this section are essential to reflect any changes in referenced documents or standards‚ ensuring ongoing compliance and accuracy․
Document Control and Revision History
This section is crucial for maintaining the integrity and accuracy of the work instruction over time․ It provides a detailed record of all revisions‚ ensuring that users are always working with the most current and approved version․ A well-maintained revision history demonstrates adherence to ISO 9001 requirements for document control․
Each revision entry should include the date of the revision‚ a brief description of the changes made‚ the name of the person who made the changes‚ and the reason for the revision․ This level of detail allows users to quickly understand the evolution of the work instruction and the rationale behind each modification․
Implement a clear document control system that assigns unique identification numbers to each work instruction․ This helps to prevent confusion and ensures that obsolete versions are promptly removed from circulation․ Establish procedures for authorizing and approving revisions‚ typically involving relevant subject matter experts and quality assurance personnel․ Regularly review the revision history to identify trends or recurring issues that may indicate areas for process improvement․ By diligently managing document control and revision history‚ organizations can ensure that their work instructions remain accurate‚ effective‚ and compliant with ISO 9001 standards․
Examples of Work Instructions
To illustrate the practical application of a work instruction format under ISO 9001‚ consider several examples across different departments․ In manufacturing‚ a work instruction might detail the step-by-step procedure for operating a specific machine‚ including safety precautions‚ setup instructions‚ and quality checks․
For a customer service department‚ a work instruction could outline the process for handling customer complaints‚ specifying how to document the issue‚ escalate it if necessary‚ and follow up with the customer․ In a laboratory setting‚ a work instruction might describe the exact steps for performing a chemical analysis‚ including sample preparation‚ equipment calibration‚ and data interpretation․
Within the IT department‚ a work instruction could detail the procedure for installing a new software application‚ including user access rights and security settings․ Each example should demonstrate the key elements of a work instruction‚ such as a clear title‚ a step-by-step procedure‚ required tools and materials‚ competency requirements‚ and referenced documents․ By providing concrete examples‚ organizations can ensure that employees understand how to create and use work instructions effectively‚ leading to improved consistency and quality in their operations․ These examples illustrate how work instructions play a vital role․
Benefits of Using Standardized Work Instructions
Standardized work instructions‚ aligned with ISO 9001‚ offer numerous benefits․ They ensure consistency in task execution‚ reducing variability and errors․ This leads to improved product or service quality‚ meeting customer expectations and enhancing satisfaction․ Standardized instructions facilitate effective training for new employees‚ accelerating their learning curve and ensuring they perform tasks correctly from the outset․
They serve as a reference guide for experienced employees‚ minimizing deviations from established best practices․ They also improve process efficiency by streamlining workflows and reducing wasted time and resources․ Clear instructions enable better problem-solving and troubleshooting‚ as employees can quickly identify deviations from the standard process․
Moreover‚ standardized work instructions support continuous improvement efforts by providing a baseline for measuring performance and identifying areas for optimization․ By documenting processes‚ organizations capture valuable knowledge‚ preventing its loss due to employee turnover․ This knowledge base can be used to refine processes and improve overall organizational performance․ Compliance with ISO 9001 requirements is also enhanced‚ demonstrating a commitment to quality management․ Ultimately‚ standardized work instructions contribute to a more efficient‚ consistent‚ and high-quality operation‚ driving business success and customer loyalty․